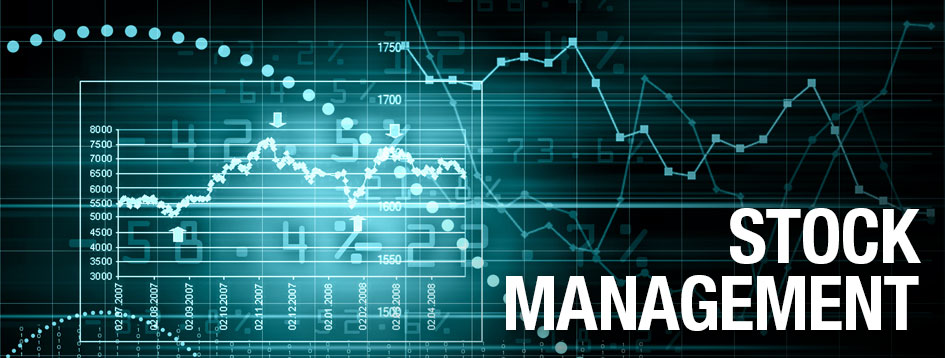
Stock Management Software
Ensuring that you always have the right parts in the right quantity available in time for workshop jobs is managed by the Stock Management module of Workshop Beaver. Its breadth of functionality allows users to proactively monitor stock levels for all items and its integration with the Purchase Ordering module allows items to be re-ordered from a recommended supplier as soon as they reach their specified re-order level.
The re-order level and re-order quantity are automatically calculated using a combination of factors selected by the user including product delivery lead time, usage history, and incoming job requirements for parts.
Multiple stock levels are available for each part including both physical and free stock so that parts can be allocated against specific jobs without fear of the stock being issued elsewhere. The Workshop Beaver Stock Management solution supports up to 99 different stock locations or depots, with stock at each depot held in its own bin location, and full audit trail and history maintained for each individual stock transaction. Serial Traceability can be used to track the movements of individual parts and is often a requirement for many of our customers.
The product classification and product grouping functionality enable stock to be associated together to suit customers specific requirements, with up to 9999 user definable product groupings being available. All information is available for enquiry and reporting purposes, and production of regular documentation for stock checking and picking lists is available.
Full bill of material functionality is provided for assemblies or sub-assemblies used in the workshop with the individual parts allocated and marked for picking against specific jobs automatically. The alternate part and product cross referencing facilities further enhance the flexibility and number of options available to ensure that stock issues to the workshop are uninterrupted and timely. Any number of ancillary services can be held as ‘Non-stock’ items (e.g . carriage charges), with full usage history recorded but no stock level recording.
This flexibility is supported with the system’s ability to value stock using standard, average or last purchase price cost, and to also hold multiple customer price lists per product, enabling stock to be sold to different customers at different prices. Inventory checks can be made on a rolling or a full physical basis, with full supporting stock-take documentation produced.
The functionality supported by the Stock Management module includes:
- Up to 9999 depots available for stock holding purposes, including inter depot replenishment.
- Stock valuation at standard, average or last purchase price and multiple sales prices per item
- Automatic stock management including stock replenishment, re-order level and quantity calculation, full integration with Purchase Order Management to generate purchase orders to preferred or recommended suppliers.
- Comprehensive and flexible product analysis provided by the product grouping and classification options, the product cross–referencing and alternate parts facilities and full bill of material component identification.
- Full history, serial traceability, audit trail and costed usage history of all stock transactions available for reporting and enquiry purposes and accessible by web enquiry for computer, tablet or smart phone.
- Accurate product data held at individual line level, such as volume, weight, shelf life, together with the ability to hold lots of descriptive and specification data against each product.
- Spares sales capability to sell spares direct to customers.
- Full or rolling stock-takes supported.
- Documentation Management – storage and generation of picking lists, stock taking lists, purchase and sales orders and other stock related documentation.